The Role of Prototyping in Product Design Process
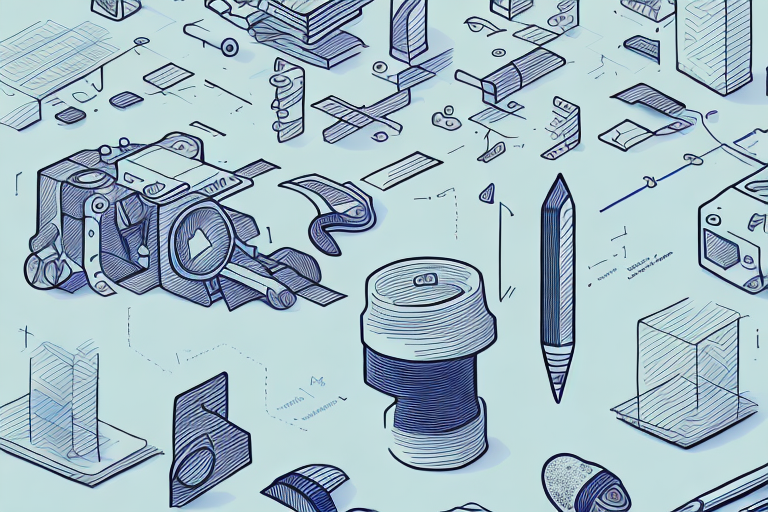
Product design is the process of creating a product that meets customer needs and expectations. It involves a number of steps, from brainstorming and researching ideas to finalizing the design and prototyping the product. One of the most important steps in product design is prototyping, which is the process of creating a model of the product to test and evaluate its design. This article will discuss why prototyping is important, the different types of prototyping, how to choose the right prototyping method, best practices for effective prototyping, and the future of prototyping in product design.
Why Prototyping is Important
Prototyping is an essential tool in the product design process. By creating a model of the product, design teams are able to quickly test and evaluate different aspects of the design and make adjustments as needed. Prototypes also enable designers to get a better understanding of how their product will work in real-world conditions. They provide valuable feedback about how customers will interact with the product. This helps designers refine their designs and make sure they are providing a quality product that meets customer needs.
Prototyping also allows designers to identify potential problems before the product is released. This can save time and money by avoiding costly mistakes that could have been avoided with early testing. Additionally, prototyping can help designers to identify areas of improvement and make changes to the design before the product is released. This can help ensure that the product is as successful as possible when it is released to the public.
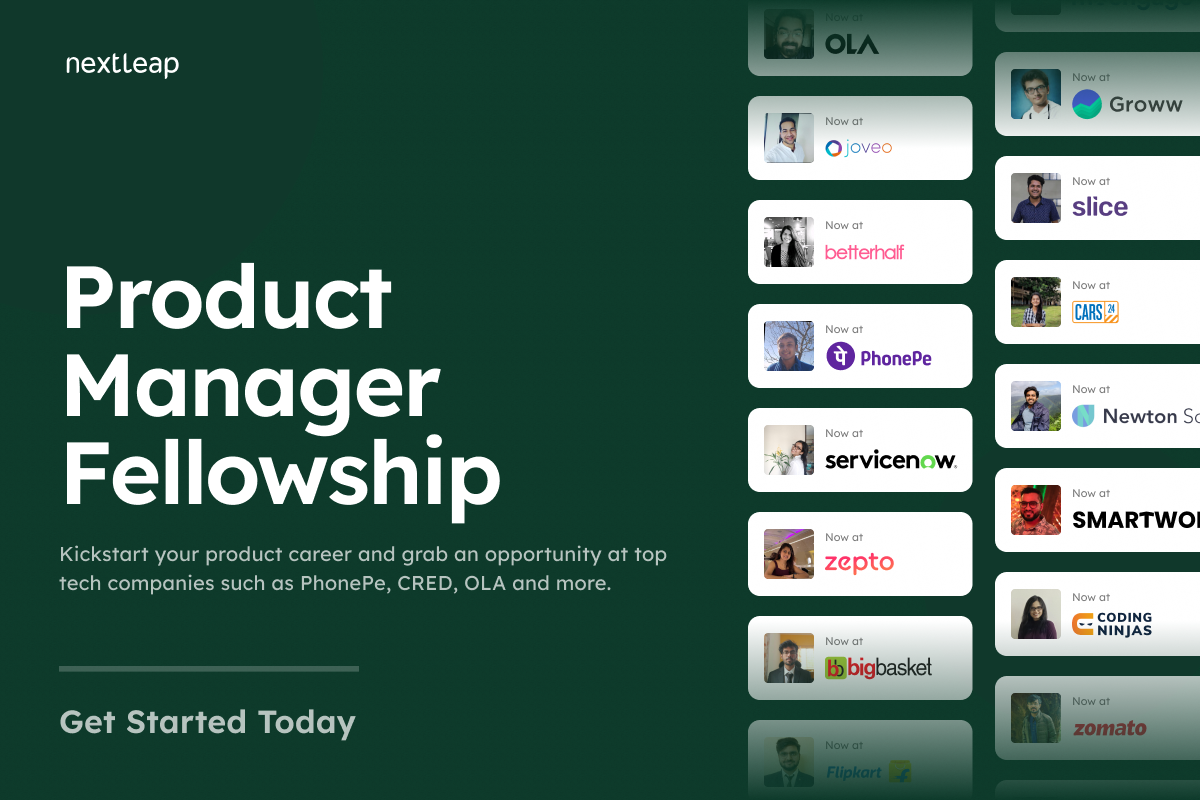
Become a Product Manager
Learn from top industry experts, get access to 1 year placement support and transition into product management at India's top tech companies.
Types of Prototyping
There are several types of prototyping that can be used in product design. Low-fidelity prototypes are basic representations of a product, typically created with paper, clay, or other materials. They are used to quickly evaluate concepts and generate ideas. High-fidelity prototypes are more detailed representations of a product and are usually created with digital tools such as 3D printing and rapid prototyping. These prototypes are used to evaluate more complex designs and can provide valuable feedback about user experience and usability.
In addition to low- and high-fidelity prototypes, there are also mid-fidelity prototypes. These are more detailed than low-fidelity prototypes, but not as complex as high-fidelity prototypes. Mid-fidelity prototypes are often used to test the functionality of a product and to identify any potential design flaws. They are also useful for testing user interactions and feedback.
How to Choose the Right Prototyping Method
Choosing the right prototyping method depends on the type of product being designed and the goal of the prototype. Low-fidelity prototypes are best used for quickly evaluating concepts and generating ideas. High-fidelity prototypes are better suited for evaluating more complex designs and getting feedback about user experience and usability. The time frame for the project should also be taken into consideration when choosing a prototyping method. Low-fidelity prototypes can be created quickly while high-fidelity prototypes require more time and resources.
It is important to consider the resources available when selecting a prototyping method. Low-fidelity prototypes require fewer resources and can be created with minimal effort. High-fidelity prototypes require more resources and may require the use of specialized software or hardware. Additionally, the cost of the prototyping method should be taken into account. Low-fidelity prototypes are typically less expensive than high-fidelity prototypes.
Best Practices for Effective Prototyping
The goal of any prototype should be to accurately represent the product as it will be used in real-world conditions. To ensure that a prototype meets this goal, it is important to consider the following best practices:
- Define clear objectives for the prototype.
- Gather feedback from stakeholders throughout the process.
- Make sure the prototype is easy to use and understand.
- Test the prototype in real-world conditions.
- Make sure to validate the prototype with users.
It is also important to ensure that the prototype is regularly updated to reflect any changes in the product design. Additionally, it is important to keep track of the feedback received from stakeholders and users to ensure that the prototype is meeting the desired objectives.
The Future of Prototyping in Product Design
In the future, prototyping will become an even more important part of the product design process. Advances in technology such as augmented reality, virtual reality, and 3D printing will make it easier to create high-fidelity prototypes with greater detail and accuracy. Tools such as machine learning and artificial intelligence will also make it easier to get feedback from users and refine prototypes quickly. The increased use of prototyping in product design will lead to higher quality products that meet customer needs and expectations.
In addition, prototyping will allow designers to test out different ideas and concepts quickly and efficiently. This will enable them to make changes and adjustments to their designs in a timely manner, resulting in products that are more innovative and cost-effective. Furthermore, prototyping will help designers to identify potential problems and issues before they become costly mistakes. This will help to reduce the amount of time and money spent on product development, resulting in a more efficient and successful product design process.
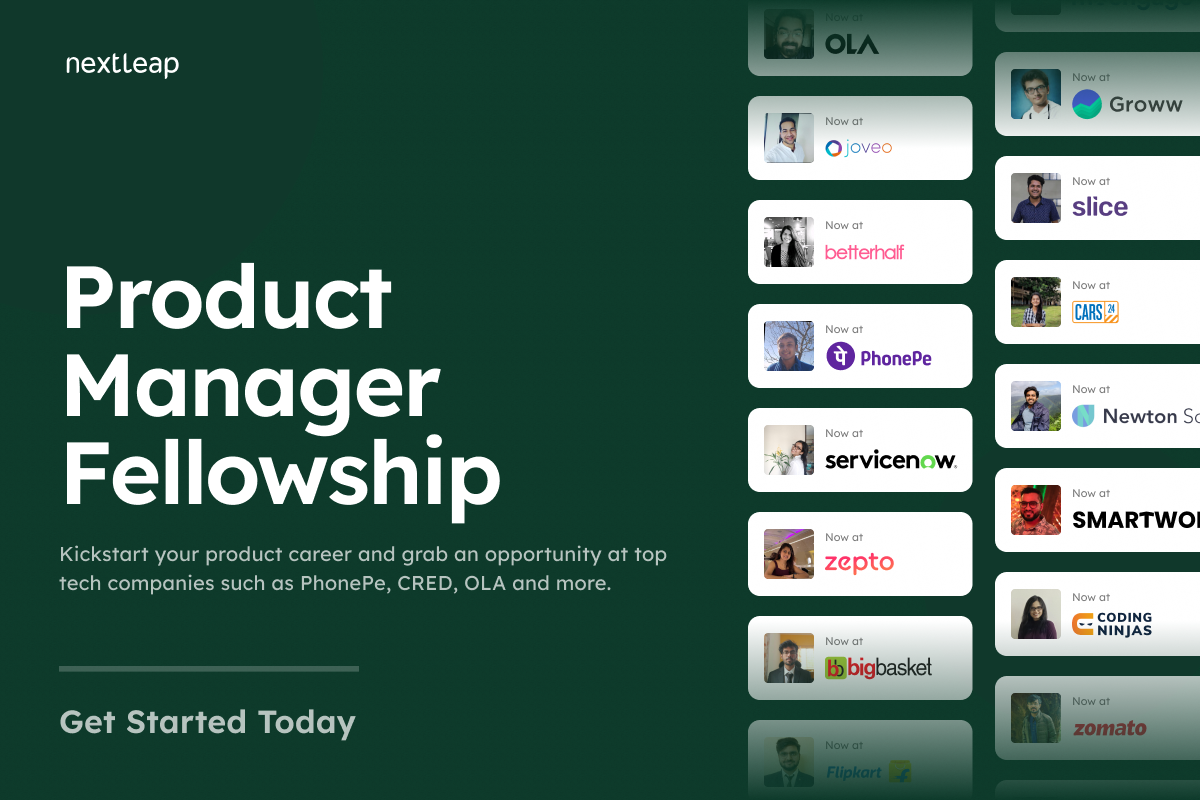
Become a Product Manager
Learn from top industry experts, get access to 1 year placement support and transition into product management at India's top tech companies.